Reducing Waste
Supporting staff to improve waste in everyday work
Have you ever looked around your place of work and considered that there are lots of opportunities to improve the value we provide to our service users by removing waste in our system? The concept of waste is defined by the Institute for Healthcare Improvement as “resources expended in money, time and/or personnel, that do not add value for the patient, family or community”[1]. Waste reduction is a key element of the programme of work that supports us to Improve Value.
Identifying and tackling waste has the potential to:
Improve quality of care
Release time for staff to focus on what matters
Reduce Cost
Increase efficiency
In April 2022, 39 members of staff took up the challenge of trying to reduce waste in their area by joining two 30-minute workshops over a week, designed to help them learn about applying the ‘8 Wastes tool’. The workshops were designed and delivered in partnership with the Financial Viability Team and aimed to equip staff from across the Trust with the knowledge and skills needed to identify and understand waste in their place of work.
The first workshop introduced the ‘8 Wastes Tool’. This tool originates from Japanese car production in the 1950s but has been widely adopted across the world and in healthcare. It categorises different types of process waste; the bits of a process that do not add value for staff, service users or those we serve. Taking the first letters of each of the 8 wastes forms the DOWNTIME acronym; to help you remember these, think of downtime as that bit of the week or the month when you might have a little time to consider whether your processes are efficient. The wastes are described below in figure one.
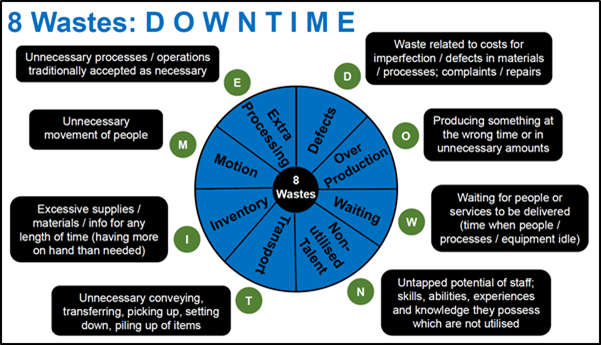
The tool is simple and easy to use, with the ability to be applied to any system or environment. A local food outlet can often be a great place to identify some of the 8 wastes in action. The next time you are in line somewhere ordering food or drink, see if you notice any of the following:
- Customers being served their food or drink but no clean tables to sit at
- Not enough staff available to process orders but too many staff preparing them
- Being given several napkins with your order when all you need is one
- Wrong orders being returned to the kitchen
- Large quantities of food being thrown away due to overproduction
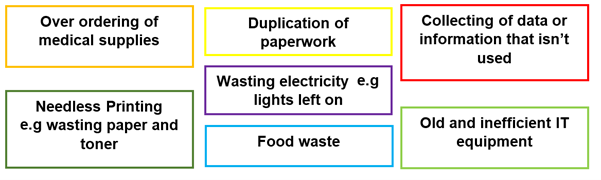
Related Resources
Related Stories
-
Reducing Salary Overpayments: A Collaborative Approach
13th January 2025
-
Reduction of Agency Staff Use in a Community Health Service
10th January 2025
-
Reduction of Transport Expenditure in Forensics
8th November 2024
Follow QI on social media
To keep up to date on the latest concerning QI at ELFT, follow us on our socials.
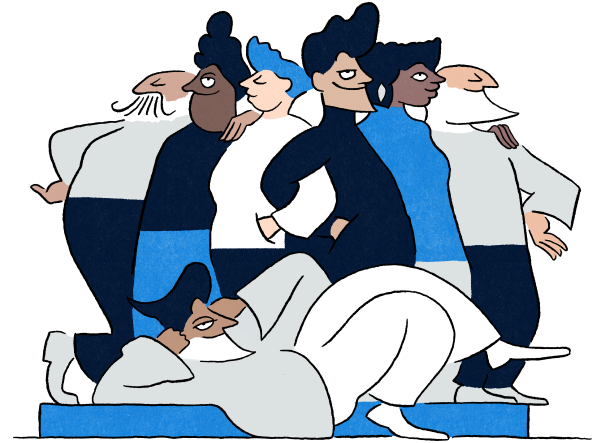