Understanding the problem
You now know the quality issue you want to focus on, so how do you start to understand the problem better?
The tools below will help you to achieve this, for example by working out the ‘baseline’ of your data. You can also consider the different ways of gathering information, such as conducting interviews and taking surveys, as well as how to involve all stakeholders in the process.
Follow QI on social media
To keep up to date on the latest concerning QI at ELFT, follow us on our socials.
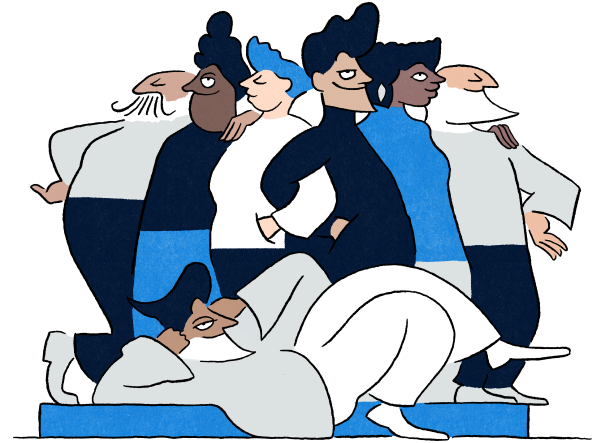